New Crushing Components
JW Bell new crushing components are the perfect solution for your aggregate needs. Our durable, high-quality range of products are designed to offer superior performance, reliability, and value. Our components have been extensively tested and proven to reduce wear and tear, increase efficiency, and reduce overall operating costs. We provide the highest quality components and unbeatable performance.
Find the right solution for your quarry below.
JW Bell Vibrating & Grizzly Feeders offer smooth, effortless material handling, making them the perfect choice for bulk material handling operations.
EIW Fine Material Washers are designed to deliver maximum efficiency and performance for your toughest aggregate washing tasks.
CONDOR Fine Material Washers
CONDOR Screw Washers offer many of the same benefits as Eagle Iron Works Classic Screw Washers. They feature the same outboard bearings, shaft dimensions, full-length curved plate, rising current plate and adjustable weirs as Classic Eagle Fine Material Screws. Washer tubs are constructed with the same material, steel thickness and matching capabilities. The main difference is that CONDOR units are built with an industry recognized Dodge TA II reducer, sized for a long life of continuous operation.
Washing fine 2.6 SG and higher solids being nominally minus 10mm or 3/8″ x 0 is the primary function of Fine Material Washers. This is accomplished by the continuous rotation of the spiral conveyor shaft and the velocity of the overflowing wastewater acting on the feed material. The rotating shaft causes the feed material to roll and tumble, which in turn provides particle-on-particle attrition. This action allows deleterious coatings to be removed from the solids and discharged with the overflowing wastewater.
Fine Material Washers are available in either single or double screw configurations, and selection is primarily a function of capacity requirements. Wear shoes can be provided in a 600 Brinell Eagle Armor iron alloy or in a premium polyurethane. Classic Eagle Fine Material Washers come equipped with a heavy-duty Eagle Gear Reducer. These gear reducers have heat-treated helical gears, triple reduction that allows 100% to 16% operational washer shaft speeds, oil bath lubrication for maintenance-free operation and drive guards as standard. Double Fine Material Screws can be manufactured in a size of 72” x 38’ with capacities up to 950 TPH.
How Fine Material Washers Work
Fine Material Washers achieve dewatering by conveying the product up an inclined tub to allow free water to drain from the material. Using a close-clearance curved plate on one side of the conveyor shaft and a drainage trough on the other side, water is allowed to drain from the product as the spiraled shaft delivers the material up the inclined curved plate. This process means less water and results in a drier final product that is more salable.
Classification is achieved by adjusting the volume of water over the adjustable-height weirs of the Fine Material Washer. For maximum material retention, the washer’s three adjustable weirs are set level to provide a low overflow velocity. For coarser mesh hydraulic splits, the Fine Material Washer’s adjustable-height weirs are offset to provide a higher overflow velocity.
Tramac TR and TX Series Breakers and Booms are the ultimate combination of power and precision, delivering superior performance for even the most demanding jobs.
Breakers and Booms
Tramac’s TR Series
Mine Duty Stationary Booms
Tramac’s TR Series Mine Duty Stationary Boom Systems are designed for high performance and increased safety over large capacity crushers.
Construction – massive, reinforced steel box sections inside and outside. “Excavator style” arched main boom section and tapered dipperstick heavily reinforced at all critical points.
Large 360 degree swing table. Rotek ball-bearing swing gear assembly, hydraulic motor with planetary and pinion gears. Shock absorbing boom base.
Protection for hydraulic line – strategic routing to prevent interference and damage. Hoses or tubes routed on top of boom.
Controls – fully proportional electro-hydraulic remote control system, dual joystick levers in aluminum box.
Hydraulic power unit – heavy duty fabricated steel assembly with tank positioned above pump, includes electric motor (voltage per specs), coupler, pump(s), filters, oil level sight gauge, tank heater, oil cooler, low level and high temperature shutoff switches, drip pan.
Automatic lubrication – available for boom, priced on request. Standard with hammer.
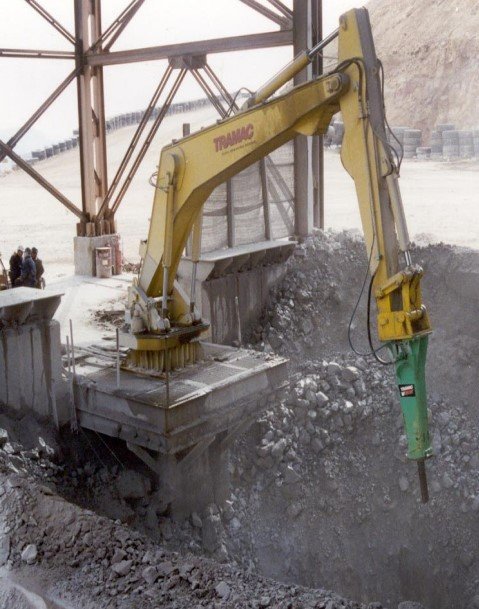
Specifications:
Tramac TX Series
Stationary Booms
Designed for the Biggest Jobs: Tramac’s TX Series Stationary Rock Breakers are extremely heavy-duty assemblies. The series is designed to carry breakers weighing up to 5555 lbs., energy classes to 8000 ft lbs., and is ideally suited for work, serving large crushers, in gyratory dump pockets, over grizzlies, underground ore passes and other high production locations where large breakers are required. These designs are the beneficiaries of many years’ experience in providing rock breaking equipment to demanding mineral mines and crushed stone producers worldwide. The TX incorporates an extra-large pedestal base with large diameter king-pins and swing post. Its heavy duty tubular steel construction is reinforced in critical areas.
Downloads:
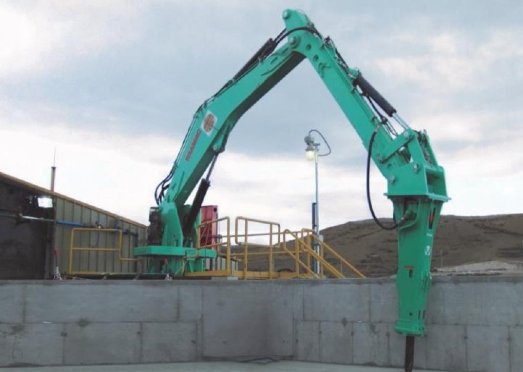
Screen Decks
Terex 6203 & 8203
The Cedarapids TSV series screens take the legendary val stroke screen to the next generation of product. These TSV series screens are built stronger, run smoother, handle more applications, and have longer life than older or copycat oval stroke screens in the market today.
Designed for Long Life
- More steel in “rock zone” for industry leading durability; 5/16” (8 mm) Grade 50 side plates are 2-times stronger than 1/4” (6 mm) standard steel; rugged computer-optimized decks with full-length bracing are unmatched
- Patented gear case baffled lubrication system along with high tolerance machined eccentric weights provide smooth running and long bearing life
- Longer HD suspension springs handle heavier loads and improve isolation to protect the screen and support structure from shock and vibration
- Patented Dual O-Ring Huck Bolt construction is “sealed for life” requiring no re-tightening or maintenance
More Production
- Enhanced Action on the Feed end provides improved
screening in the heavy load zone - Variable slope installation from zero to 10 degrees allows matching the slope to the application to minimize bed depth as well as larger screen openings up to 6”
- High G-force, high efficiency oval stroke motion adjusts 3-ways (speed, stroke angle, stroke magnitude) to optimize performance
- Patented optional bottom deck deflector platesboost screen efficiency by up to 12%
- Medium scalper option increases feed size from 10” to 14” (254 to 355 mm); option includes side liners/with 6” side extensions to contain larger stones
- High Speed Variable slope (HSV) option increases operating speed up to 1000 rpm with reduced stroke compared to standard screen
Reduced Cost of Ownership
- Maintenance-friendly features include the patented low maintenance surge damper system; bolt-on upper and lower spring guides; “tool-less” oil check sight glasses; sidewall hand access system for wire cloth clamp bars; bottom deck feed curtain; optional magnetic deck wear liners, optional “TOPS 2.0” oil filtering system.
- Patented “flow-through” lubrication system and patented “sealed-for-life” double O-ring construction provides maximum equipment life
Specifications:
Maximum stroke (stroke can be reduced by removing weight plugs) | 3/4" 19 mm |
Recommended speed range | 675 - 875 rpm |
Maximum feed size, standard decks | 10" 254 mm |
Maximum feed size, medium scalping decks | 14" 356 mm |
Maximum drop of feed | 18" 457 mm |
Discharge lip liner thickness (AR plate) | 1/4" 6 mm |
Feed box liners, standard (AR plate) | 1/4" 6 mm |
Feed box liners, medium scalping (AR plate) | 3/8" 9.5 mm |
Bearing size (516 models) | 130 mm |
Bearing size (616 and 620 models) | 160 mm |
Bearing size (720 and 820 models) | 190 mm |
Wire cloth length, standard | 4' 1219 mm |
Wire cloth length, optional (620 and 720 models) | 5' 1524 mm |
Dedicated to Your Industry
Find the right aggregate processing solution to improve your productivity
Search Our Site
How can we help your process work the best for you?
Call our aggregate specialists today, 319.362.1151.
Contact Us For All Your Aggregate Needs